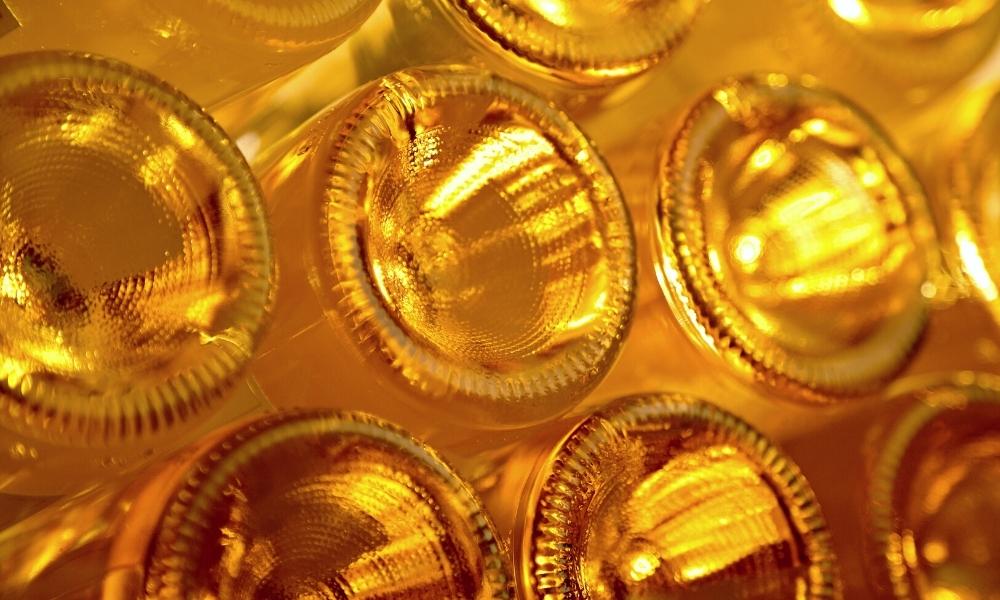
From 16 FTEs to 10: the streamlining process increases productivity by 40%.
In this case study, Maxwell's intervention was necessary for both the Italian and non-Italian divisions of the group operating in the soft beverage sector.
In the Italian case, the aim was to improve the efficiency of the man/production ratio. In fact, the system previously used involved several men manning a single phase of the filling or packaging line, creating a not inconsiderable waste of time.
On the other hand, for the foreign plant, an activity aimed at reorganising hierarchies and personnel was carried out: in fact, 150 excess units were found.
Company
The customer is a group that works in the soft drinks sector and employs about 4000 people. The average turnover is EUR 1.71 billion.
Italian Case
Goal
The aim of the project was to increase human efficiency in the filling and packaging department of two product lines and to improve the involvement, collaboration and development of its staff.
Therefore, it was necessary to:
- Make human work in the production lines more efficient.
- Improve document management processes.
- Improve personnel handling processes in the production facilities.
As Is
In the Italian plant, for the two production lines, there was an inefficiency of personnel working on the filling and packaging lines. In fact, a total of 16 employees were engaged, eight per product line, organised by 'fixed station'.
The concept of 'phase worker' prevailed: the individual manning only one phase of the entire process, not moving to the previous and/or next phase, let alone the parallel production line.
This static nature meant that much of the employees' time was spent waiting for their turn.
To Be
- Application of lean thinking methodologies in production, starting from the basis of time and methods.
- Relayout (light) of lines.
- Redesign of production layouts by introducing the area operator concept.
- Introduction of visual management in the department.
- Definition of 'rules of engagement' for operators and operating instructions and management of the entire training process.
- Modification of the organisational structure of line managers and department heads.
- Analysis of the technical availability of plants and management of technical interventions geared towards this goal.
- Revision of the Wcm model with a view to problem solving and continuous improvement.
- Team coaching and personal training on certain key figures.
Among all these operations, it is important to specify the concept of the 'area operator': the operator can move along the same production line on both the previous and the next stage and in the absence of physical obstacles, can also move to the other production line, making the use of time more efficient.
Benefits
- Reduction from 16 FTEs to 10 FTEs per shift on the two production lines.
- Increase in man productivity by 40%.
Non-European case
Goal
The objective was to reorganise supply relationships and downsize the division of labour. In fact, due to an inadequate organisation and the presence of a dense hierarchy, it was necessary to rationalise activities and increase the efficiency of the entire plant (6 filling lines, Blending, Warehouse & Logistics, Quality).
As Is
The foreign plant had 500 employees, with the presence of redundant staff. In fact, a high proportion of external employees, i.e. from companies with external contracts, carried out handling and packaging operations, also in separate areas. In addition, there were a large number of employees for manual activities and a fair share of company executives: there were many hierarchical levels.
To Be
- The concept of area operator was introduced, but above all, there was a rationalisation and restructuring, in fact, the number of employees fell from 500 to 150.
- Assessment
- Application of lean thinking methodologies in production, starting from the basis of time & methods
- Relayout (light) of lines
- Redesign of production layouts, through the introduction of the area operator concept
- Introduction of visual management in the department
- Definition of 'rules of engagement' for operators and operating instructions and management of the entire training process
- Modification of the organisational structure of line managers and department heads
- Analysis of the technical availability of installations and management of technical interventions geared towards this objective
- Revision of the Wcm model with a view to problem solving and continuous improvement
- Team coaching and personal training on certain key figures.
Benefits
- from 245 to 180 FTE (reduction of 150 out of 500 employees)
- + 37% increase in man productivity